Product Development with Unique Technologies
NISSEI designs products based on the idea that factory floor is the center of molding businesses and with out-of-the-box thinking that no other competitors have. These innovations could not be materialized without making efforts to reduce environmental impact. Here are some examples.
Hybrid Type Injection Molding Machine
When other injection molding machine makers in Japan shifted their strategies towards making all-electric presses as their main products, NISSEI developed a hybrid type injection molding machine, which uses a servomotor to drive the hydraulic pump. NISSEI offers both all-electric and hybrid drives as their two pillars of fundamental technologies. All-electric presses feature a toggle type clamping mechanism, which achieves faster cycles. Hybrid presses feature a direct pressure clamping mechanism, which transmits clamping force evenly to the mold to achieve higher product qualities. By utilizing the hybrid technologies, NISSEI developed an energy-saving molding method “N-SAPLI.” It offers a variety of benefits, such as reducing molding defects (short shot, sink mark, etc.), achieving faster cycles, improving the longevity of machines/molds, and reducing the frequency of maintenances. To elevate NISSEI’s hybrid technologies to the next level, the hybrid type horizontal injection FWX Series was developed. The FWX Series machines are two sizes more compact than the conventional machines, allowing 30% as many machines can be fit on a given space. All of the hybrid low-floor typer vertical TWX Series machines offer 1m mold mounting height regardless of tonnages, which is 30% lower than that of conventional machines. The series has been highly received by the users for its user friendliness.
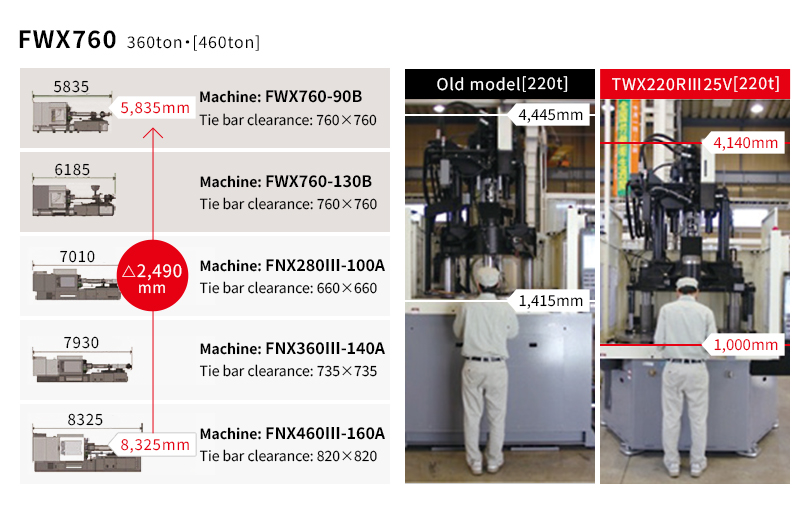
Efforts in Utilizing Eco-Friendly Materials
Marine plastic pollution is widely discussed today. NISSEI has developed number of molding technologies to process eco-friendly materials since early on.
-
Dissimilar material mixing technology was developed in order to reduce the amount of resin to be used.
-
In 1993, NISSEI developed a blending molding technology, which mixes walnut powder and biodegradable resin directly on a machine, and it was revealed at a trade show. In the same year, NISSEI also developed a sandwich molding technology, which uses recycled material as the core and forms outer layer with virgin material.
-
Practical application of pulp molding, which uses pulp and starch as the main ingredients, was developed.
-
Biodegradable PLA molding method “N-PLAjet (heat-tolerant series)" was developed and has been used for the productions of tableware.
-
Biodegradable PLA molding method “N-PLAjet (thin-wall series)" was developed. Molding of thin-wall champagne glasses (thinnest part: 0.65mm) was demonstrated and well received at K-2019 in Germany.
IoT and DX
Since the NC-NET, a group management system of injection molding machines, was released in 1984, NISSEI has been working on implementing IoT and DX (Digital Transformation) in their molding machines. Currently, NISSEI is promoting “N-Constellation,” which utilizes an injection molding machine as a network hub to connect auxiliary equipment by incorporating data communication standards, such as OPC-UA and EUROMAP. In addition, NISSEI has been developing cloud-based monitoring/controlling systems and digitalization of molding conditions.
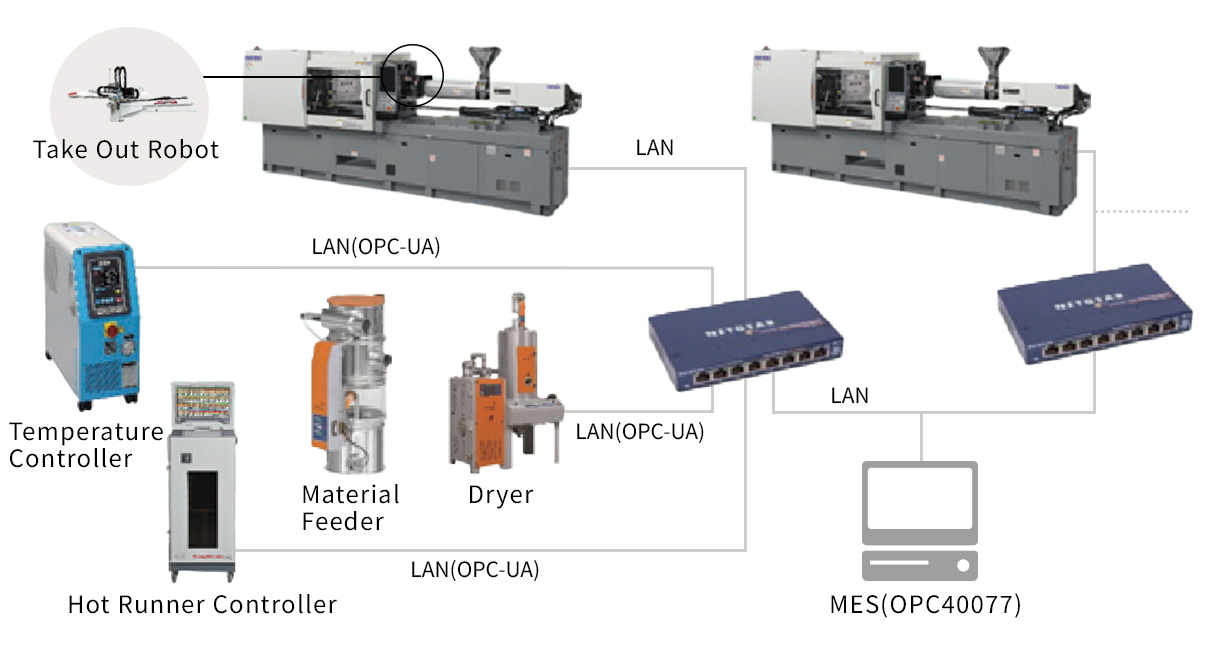